Ford puts every Ranger and Ranger Raptor through thorough checks
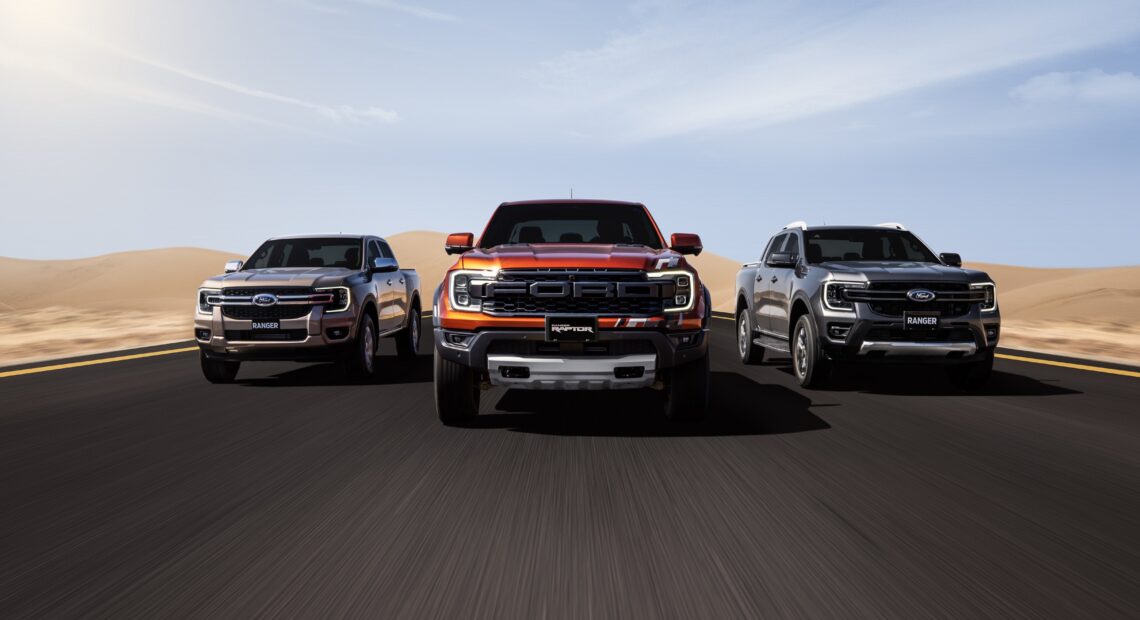
Before handing over to customers
Ford’s rigorous quality control process ensures that every Ranger and Ranger Raptor is ready to meet customers’ expectations worldwide.
According to Sundarrajan Venkatesan, Director Of Quality and New Model Programmes at Ford International Markets Group, the keen eyes and steady hands of the customer acceptance line (CAL) inspectors are integral in providing the final seal of approval on each vehicle.
The customer acceptance line is a six-step process that every Ranger and Ranger Raptor undergoes before being shipped to global markets. This extensive procedure covers a variety of inspections, including artificial intelligence checks, paint and panel assessments, interior and lighting evaluations, electrical diagnostics, and a test on a 320-metre-long squeak-and-rattle track designed to simulate various driving conditions.
The six steps of the customer acceptance line:
- Darkroom inspection: In this step, all lights are turned off, and inspectors carefully check the head and tail lamps, instrument cluster, SYNC screen, and all interior lighting for brightness and alignment.
- Hands-on inspection: inspectors then run their hands across every vehicle surface, ensuring flawless contours and the panels aligned correctly. They press, poke, click, and pull every button, switch, and control, meticulously verifying their functionality.
- Systems check: A thorough diagnostic test ensures all electrical components are connected and functioning correctly.
- AI eyes: Ford’s mobile artificial intelligence vision system (MAIVS) uses advanced algorithms to scan the vehicle’s exterior. This technology helps detect flaws, such as missing or misaligned badges, ensuring the vehicle’s appearance is flawless before shipment.
- Rainstorm simulation: The “Leak Test” simulates a heavy monsoonal downpour with high-pressure water jets. The vehicle is blasted with water from all angles, and inspectors assess every light and seal for watertightness. The water used in this process is treated and reused for further tests, enhancing sustainability.
- Squeak-and-rattle track: The final test takes place on a 320-metre-long track featuring a variety of surfaces, including cobblestones and angled iron plates. This track simulates real-world driving conditions, testing the suspension and steering and ensuring no unwanted squeaks or rattles. The inspection ensures that every vehicle is mechanically sound and free from issues affecting its performance on the road.
Image: Ford’s six-step procedure reflects its commitment to sustainable and innovative practices in the automotive industry. Credit: Ford